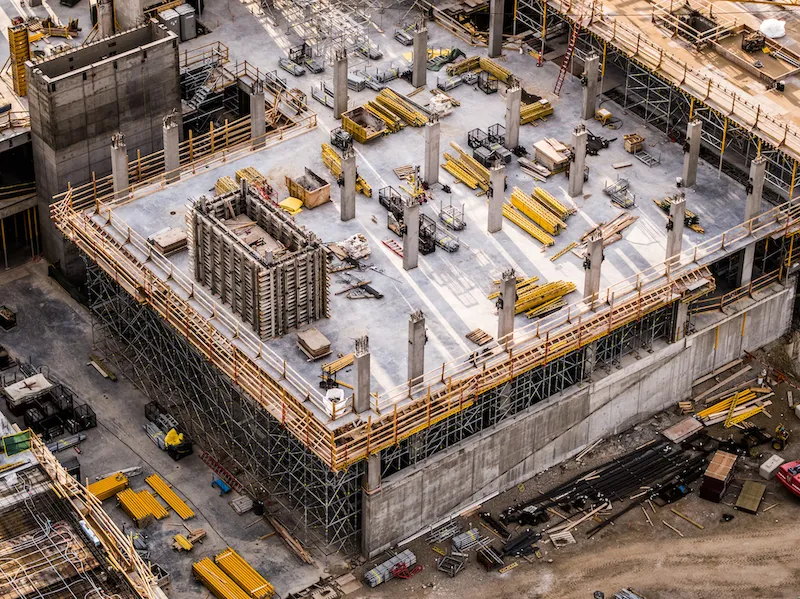
How to Track Consumable Inventory Used for Construction
Inventory management for construction companies is typically focused on tools, equipment, and building materials. However, consumables and other quantity(bulk) items are an often-overlooked inventory segment where the budget impact can be much larger than tools.
Consumables are products you provide your employees that you don’t expect to get back as they get “consumed” on the job. Examples include anchors, caulk, tape, nails, and power tool accessories like drill bits, grinding wheels, or saw blades.
Quantity items, sometimes referred to as “bulk” items, are like consumables, except these items are expected to be returned. A few examples are caution cones, forms/stakes, hammers, shovels, as well as power tool accessories that are expected to last beyond the project you are assigning them to. From an inventory perspective, it's important to understand the quantity assigned to a project or person, but tracking the specific item is not as critical as a power tool.
Despite representing a significant proportion of inventory value, tracking consumables and quantity items often go overlooked as the total cost of these items is not well understood. For example, an SDS Max rotary hammer can cost anywhere from $400 to $1000. However, a contractor will use $2000 to $5000 in carbide bits over the life of that tool (and that’s assuming you only use one size and don’t lose or damage any bits, so the actual spend could be 2-3X that number).
Tracking consumables will provide insight into a large portion of your inventory spend that is most likely overlooked today. This can help you recognize opportunities to purchase these items more efficiently, saving time and money. Managing inventory levels will avoid unnecessary project delays from running out of these small but critical items. However, it's important to find a consumable tracking system that doesn’t slow down your people in the process.
Choosing the best consumable inventory management software for your business:
-
Ideally, you are already using a tool-tracking app that uses a similar process to track consumables. This is key so your employees can get up to speed quickly and don’t have to learn/remember an additional app or workflow. (They can just follow a similar process to how they are tracking tools)
-
Just like tracking tools, consumable inventory management should allow you to track available inventory in the shop as well as consumable inventory that’s stored on a job site prior to assigning the items to an employee. This is a key feature that many legacy/generic inventory management software systems do not have if they are not focused on the construction industry.
-
The system should provide real-time inventory, including on-hand quantities in all inventory locations as well as usage by employee. This visibility is critical to ensure you don’t run out of stock on an item that could delay your project.
-
Your consumables management system should be able to track usage and spend by project. This will allow you to bill your customer if desired and help you better understand your true project cost for future bids.
-
Some systems offer additional features like PO creation and automated re-ordering from vendors. While these features can be useful, they often make the system complex and expensive. Weigh your budget and available resources before opting for such features.
-
We recommend finding a solution that includes a mobile app for field employees and a web admin app compatible with your PC to manage these sku intensive product lines. It will be important that both you and your employees can view available inventory as well as consumed inventory so there is transparency and accountability.
-
Finally, consider a system that allows code scanning of bar codes and QR codes. For consumable items as well as other quantity items (bulk items that you provide to employees but do expect to get back), you can quickly scan the bar code on the item/package to identify the item and transfer it to an employee quickly. While some companies offer separate scanners, this is unnecessary as your phone is highly capable of scanning codes if you have the right mobile app.
Properly managing consumable and quantity inventory can lead to substantial cost savings and improved efficiency in your construction business. By using the right inventory management system, you can gain better control over your resources and increase your project's profitability.
TOOTLRIBE Pro is a simple consumable inventory management system designed specifically for construction contractors.
Consumables and Quantity items are added using the same process as adding a tool. When you add the item, just enter a quantity greater than one and then check the consumables box if you don’t expect these items to be returned. When transferring/assigning the items to employees and/or projects, just select the quantity to be assigned along with the person and project, then press transfer.
You can then Track and view the inventory on your phone or PC. If the item was indicated as a consumable, your on-hand inventory will be deducted when transferred. You can review the consumed inventory by filtering tools by “consumed” on the mobile app or on the web admin. If the item was indicated as a quantity item, you can filter by the item, person, and/or project and see the inventory assigned in addition to the available inventory.
Contact us to learn more or schedule a demo. We are ready to help you start managing your inventory, including tools, equipment, consumables, and other related inventory.